Hale Engineering was engaged in enhancing the emergency vent system at an incineration plant by integrating a new valve set into the electrical and control systems. While the project initially focused on wiring the valve actuators to the plant’s control systems, the team encountered unexpected challenges that required additional problem-solving, including resolving motor control issues and improving system visibility.
Challenge
This project presented several critical challenges:
- Incorrect Circuit Diagrams: The provided wiring diagrams did not align with the actual system setup, requiring our team to trace and verify every PLC I/O connection to ensure proper integration.
- Motor Control Wiring Errors: Wiring issues with the bag filter motor and another motor prevented proper operation and control, posing a significant risk to plant efficiency.
- Limited SCADA Visibility: The existing SCADA system lacked the elements required to provide operators and management with real-time insights into the operation of the emergency vent system.
- Restricted MCC Room Access: Operators were unable to manage the bag filter motor locally, leading to operational delays and reliance on the MCC room for routine tasks.
Our Approach
Hale Engineering employed a systematic and flexible approach to address the project’s challenges, focusing on electrical wiring, fault resolution, SCADA enhancements, and thorough testing to ensure system reliability.
Electrical Wiring and Integration
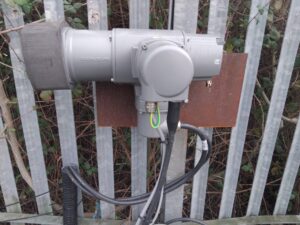
Auma Valve wired and ready for commissioning, with local control corrected to ensure proper operation of the bag filter
The project began with a site assessment to evaluate the installation and integration requirements for the Auma valve actuators. Our team installed and terminated all necessary power and signal cables, ensuring the actuators were properly connected to the plant’s PLC and SCADA systems. Additionally, the PLC I/O connections were carefully verified and corrected to ensure seamless integration and accurate signal mapping with the control systems.
Fault Resolution
During the project, our engineers identified inaccurate PLC wiring that affected the functionality of the bag filter motor and another motor. These errors were rectified by mapping the PLC outputs correctly, and restoring the motors’ operation. To enhance operational flexibility, local motor control was enabled through the operator interface, eliminating the need for constant access to the restricted MCC room.
SCADA Enhancements
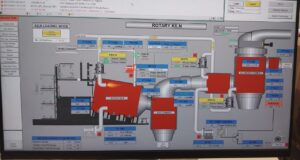
Updated SCADA interface displaying the penstock valve integration for improved monitoring and visibility.
To improve system monitoring and feedback, new SCADA elements were implemented, including visual indicators and alarm systems. These enhancements provided operators with actionable insights and management with real-time oversight capabilities, ensuring the system’s reliability. Furthermore, the SCADA interface was upgraded to enhance visibility for the emergency vent system, allowing operators to monitor and verify valve operations during simulated emergency scenarios.
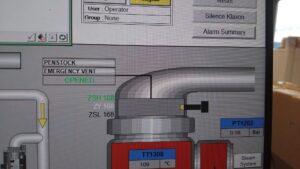
Simulated penstock signals tested on the updated SCADA system, ensuring operational readiness ahead of valve commissioning
Testing and Documentation
Comprehensive testing was conducted to ensure the accuracy of the corrected PLC wiring, motor control functionality, and integration of the valve set with the SCADA system. Live operational trials were performed to validate the system’s reliability under real-world conditions. Upon completion, detailed documentation was provided to the plant’s maintenance team, including updated wiring diagrams, SCADA updates, and a summary of modifications to support future troubleshooting and maintenance.
Outcome
The project successfully delivered:
- Restored Motor Functionality: The bag filter motor and other systems were fully operational, with local control restored for greater operator flexibility.
- Enhanced SCADA Visibility: Operators and management gained real-time monitoring capabilities, ensuring transparency and reliability.
- Improved Operational Efficiency: Reducing reliance on MCC room access streamlined daily operations.
- Future-Proof System: Clear documentation and updated configurations positioned the plant for long-term reliability.
Future Recommendations
To further enhance reliability, Hale Engineering advised the plant to update all wiring diagrams to reflect the corrected configurations. Regular electrical audits and operator training were also recommended to proactively identify issues and maintain system efficiency.
Conclusion
This project highlights Hale Engineering’s ability to tackle complex technical challenges while delivering practical, long-term solutions. Our commitment to precision, innovation, and reliability ensured the incineration plant’s systems were restored and enhanced to meet current and future operational needs.
Contact Us
Need an engineering partner to solve your toughest technical challenges? Contact Hale Engineering today to learn how we can support your operational needs.
Phone: +44 20 8154 6102
Email: info@hale-eng.co.uk