Within industrial automation and engineering, innovation is a constant necessity. Engineers must adapt, enhance, and sometimes even resurrect aging systems to maintain efficiency and competitiveness. This case study is Hale Engineering’s task in reviving a discontinued bag house controller for compressor blow down valves.
The Bag House and Its Vital Role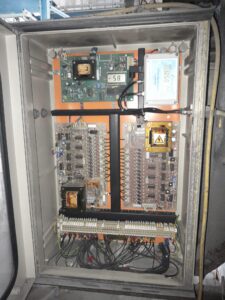
A bag house, in an industrial context, is a critical component used to filter the air from various processes, including incineration. In this specific case, the bag house played a pivotal role in removing contaminants from the air, which were primarily associated with the incineration process.
The Role of Lime and Blow Down Valves
To optimise the filtration process, lime was introduced into the bag house in the form of bags. These bags worked as filters to capture and neutralise impurities from the air. Over time, the lime would accumulate on the bags, gradually reducing their efficiency. To combat this issue, blow down valves were employed, delivering quick pulses of air to dislodge and clean the lime off the bags.
The Discontinued Controller Dilemma
The functionality of this bag house system relied heavily on a controller. However, a significant problem arose when it was discovered that the original bag house controller had been discontinued and was no longer supported. This created a major challenge for the operation of the facility, as maintaining efficiency and reliability in the absence of proper support for such a critical component was extremely difficult.
Hale Engineering’s Solution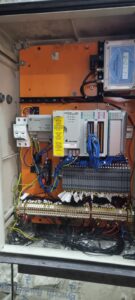
Recognising the urgency of the situation, Hale Engineering took on the task of upgrading the bag house controller. They decided to replace the obsolete controller with a modern Allen Bradley controller. This required a meticulous approach, ensuring that the new controller could seamlessly integrate with the existing panel and circuits.
The Software Challenge
Beyond the hardware upgrade, the team at Hale Engineering faced another substantial hurdle – replicating the complex process of lime filtration and bag cleaning using software. This involved writing custom software to control the new controller effectively.
Commissioning the Revamped System
Once the hardware and software components were successfully implemented, the system required thorough testing and commissioning. The team at Hale Engineering ensured that the bag house controller worked flawlessly and efficiently in its upgraded state.
Uncovering Pre-Existing Faults
In the course of their work, Hale Engineering engineers also made a surprising discovery. While upgrading the bag house controller, they uncovered pre-existing faults in the compressor valves, which were responsible for delivering the quick pulses of air to clean the lime off the bags. These issues could have been contributing to the reduced efficiency of the bag house system.
Fixing the Compressor Valve Faults
Addressing these compressor valve faults was not initially part of the project’s scope. However, the Hale Engineering team provided a comprehensive solution to rectify these issues as well. This ensured that the bag house system could operate at peak performance once again.
In conclusion, this successful case study demonstrates the importance of adaptability and innovation industrial automation and engineering. By reinvigorating a crucial system that was once abandoned, the team have restored operational efficiency for the bag house.